Minor disruption, expensive production downtime

How global manufacturers protect their production networks
A small IT failure can have big financial consequences. In highly automated industries like automotive and food production, network infrastructure failures can bring operations to a standstill, causing millions in losses per hour.
This case study reveals how two global manufacturers successfully gained full control over their IT infrastructure and significantly reduced operational risks with DC Vision.
Untracked IT changes – A costly risk
Many manufacturing companies struggle with decentralized IT infrastructure. Frequent on-site modifications—such as replacing network components—are often not documented, leading to:
- Extended troubleshooting time when failures occur
- Unclear network topology, making maintenance inefficient
- Higher downtime costs due to delayed issue resolution
Without real-time visibility, identifying affected components during an outage can take hours, resulting in unnecessary production losses.
Fast-tracking IT resilience with DC Vision
By implementing DC Vision, both companies achieved:
- Complete documentation of all IT racks across multiple locations
- Instant identification of network components in case of failures
- Significantly reduced downtime and operational risks
Using AI-powered image recognition, IT teams were able to scan and document a full server rack in less than 10 minutes, ensuring an always up-to-date asset inventory.
Discover in this case study:
- How to monitor and analyze your IT infrastructure in real time
- Seamlessly connect the logical and physical structures of your systems
- Minimize downtime and improve IT asset management efficiency
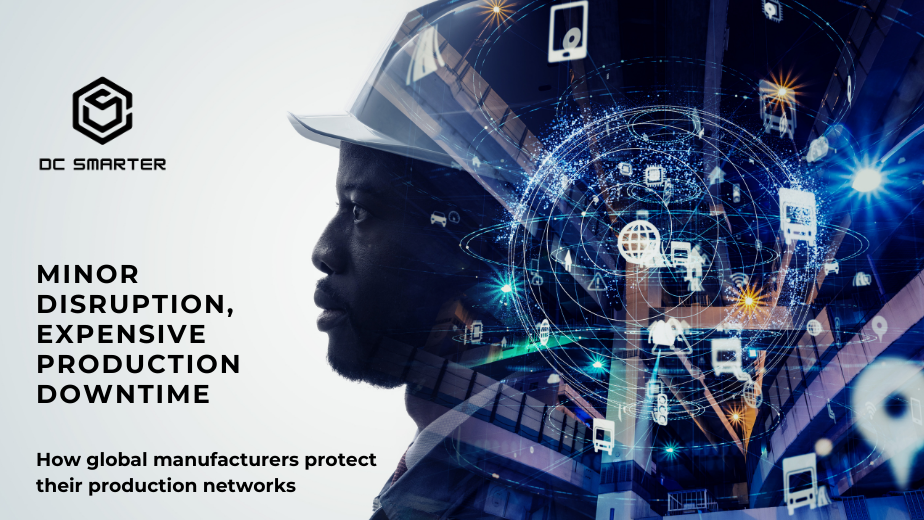